
The will be CAN networked, allowing integration into other on-board systems.
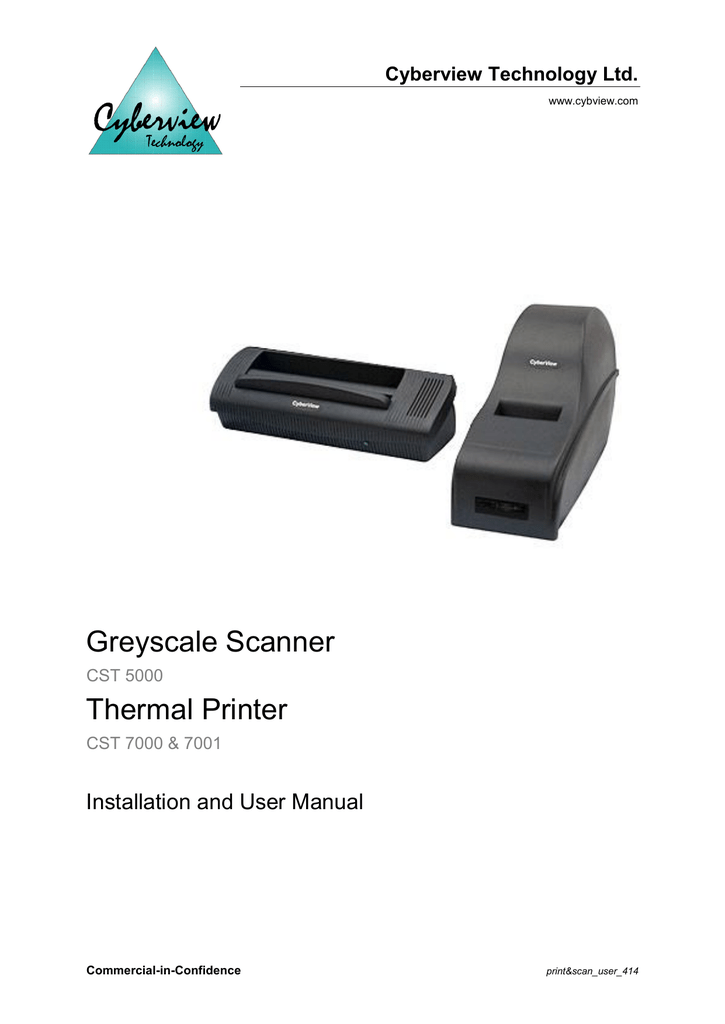
Reducing vehicle weight, reduced emissions and increasing fuel economy is a common theme in today’s automotive world. One manufacturer claims it saves as much as 16 pounds on a full-size SUV/pickup. Another advantage is that the vehicle manufacturing process is streamlined requiring only one hydraulic and one electrical connection on each rear-brake assembly. It eliminates the need for brake cables and the hardware and packaging they require. There are several advantages to the caliper- integrated EPB design setup. Most systems will use a gear reduction drive to provide the needed force with a small electric motor. This electric motor mechanically forces the caliper piston out to provide the necessary clamping force on the rotor. The caliper-integrated design incorporates a bidirectional electric motor on each caliper. The cable puller design has been popular and is still being used, but the caliper-integrated design has gained popularity and its simplicity will likely make it the favorite. Some manufacturers provided access ports and in some cases tools to release the cables.įor example, Range Rover had a special cable release under the center console.
#NISSAN DATA SCAN TIMING MODE MANUAL#
Many of the first designed cable puller units provided some form of manual release mechanism in the event of a motor failure. The CAN connected cable puller EPB controller/actuator can be tucked somewhere under the car or even in the trunk. Existing cable style brake calipers or parking brake shoes can easily be adapted to use the cable puller EPB. The advantage of this style of EPB system is that it lends itself to be an add-on solution, using some existing parts. This bidirectional motor supplies the pulling force to the brake cables that run to either the rear calipers or the parking brake shoes (a drum-in-hat rotor style). The cable puller design motorizes the traditional handbrake or parking brake pedal function by using a bidirectional motor. It is important to note that neither system will function if there is no vehicle power. There are two common designs used in the EPB system: the cable puller system and the caliper-integrated system. The reasons behind EPB and the two common designs This provides the EPB system the ability to use and share information from the other modules on board for a multitude of functions. Some earlier versions had a stand-alone ECU, but most of today’s versions of the EPB system are almost always integrated into the vehicle’s controller area network (CAN) architecture. The EPB system requires an electronic control unit (ECU). The system uses an electric switch to activate and deactivate the parking brakes.
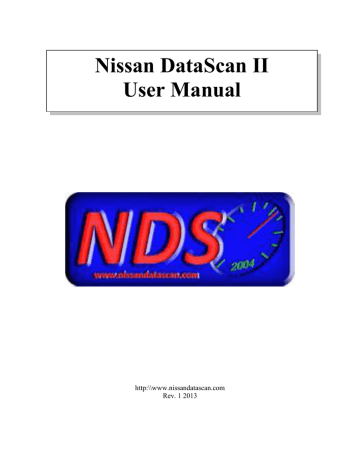
It is even showing up on popular pickup truck models.ĮPB eliminates the mechanical connection between the operator and the parking brakes it’s now operated by wire. One major worldwide brake supplier has now produced over sixty million caliper-integrated EPB units (the parking brake motor is part of the caliper) and has moved on to their fifth generation of EPB designed products.
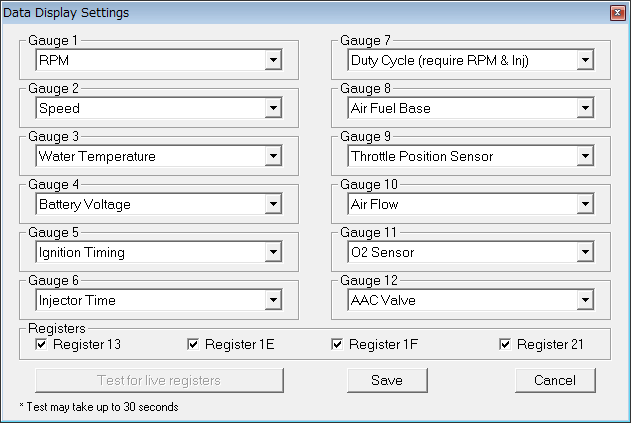
It’s been on some vehicles since the late 1990s, but there seems to be a surge to move to the EPB system on many new models. The use of an electric parking brake (EPB) system is not new. This article explains the current systems and provides insight regarding understanding and troubleshooting these non-mechanical approaches. The advent of electronic parking brake (EPB) systems offers advanced technology but can pose challenges for the service technician.
